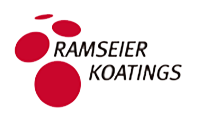
+852 2363 2511
Metallic powder coating has emerged as a revolutionary surface finishing technique, adding a touch of glamor and sophistication to diverse materials. Dull, lifeless coatings are passé indeed; metallic powder coating is ushering in a shimmering era of endless possibilities.
It’s quickly replacing anodized and fluoropolymer resin in the face industry as an aesthetically superior finishing for windows, doors, sun shading, and other components. If formulated and applied correctly, this powder coating will improve the aesthetics of your face to the highest degree possible.
The alluring power of metallic powder coating extends beyond captivating beauty. Here are the best reasons to get going with this trend.
● Visual Appeal like No Other
● Can Stand the Test of Time
● Eco-friendly and Sustainable
● Versatile and Customizable
● Money Saving
Metallic powder coatings are available in a range of popular effect pigments, ensuring customers get precisely what they want. Here's a glimpse into the most common types:
● Aluminum Flake: It consists of various sized and geometrical shaped aluminum flakes that create a sparkling pearlescent effect. The intensity of the metallic shimmer depends on sequin size and concentration.
● Mica Flake: Mica flakes do not have the reflective ability of aluminum metallic but instead show a softer albeit less pronounced sheen. By nature, they have a fine iridescent appearance which results in a classier and more refined chrome finish.
● Metallic Pigments: These are finely powdered metal particles used to create a more uniform, metallic finish. These effect pigments are the best option for bolder, mirror-like effects and use in automobile and architectural applications.
● Hybrid Combinations: Sometimes metallic powder coating contains different types of metallic pigments and flakes combined for nuanced special effects as specified by the customer. These combinations are hybrids in nature allowing customers to experiment with their creativity
Powder coatings containing metallic and special effects can be made in two ways. One by a straightforward dry blend method, and the other via a bonding procedure. Both metallics have the ability to shimmer. What separates them is the method of manufacture.
This procedure creates unbonded metallic powder coating by simply adding and combining the metallic and special effect material(s) with the base powder. Compared to how bonded metallics are made, this method is easier, faster, and less expensive.
Unbonded metallic powder is generally available to purchase in smaller units than its bonded counterpart. Manufacturers usually offer these powders at a lower price than bonded ones and even ship out orders faster.
That being said, one will have to be keen when spraying unbonded metallic powder coating or cleaning up afterward. Since the powder particles and metallic effects have not been fused together, the coat can end up rough and inconsistent. Even the sparkles themselves can disperse unevenly or gather at the edge of the surface
Unlike dry blending where the manufacturer simply combines base powder and effect pigments without any fusion, bonding is a nuanced process involving mechanical fusion technology. The manufacturer begins by heating the base powder to make it sticky then adds the effect pigments (aluminum, mica, or metallic). Of course, the pigments will fuse with the powder particles because the latter has been made sticky. The coat spreads evenly on the object’s surface and offers much better performance.
Naturally, it’s much easier to spray bounded metallics powder than the dry blended kind. The fused powder and metallic effects simply roll and stick onto the surface for a much smoother, cleaner, and even finish. It’s the reason most architects and manufacturers recommend powder coating for metal window facades.
Moreover, when it comes to recyclability, bonded metallic powder has a higher scrap value. Any fallen or leftover powder can be collected for later use and save on the costs of having to buy new powder.
That being said, bonded metallic powder generally costs more than the one produced via the dry blending technique. This is because the bonding process involves an extra number of steps that translate into extra costs on the part of the manufacturer. They also don’t make it in smaller batches, meaning you cannot order a small amount.
But, in the long run, it’s more cost-effective to go with bonded vs unbonded. Yes, at first, it will punch a hole into your budget but you get a high-quality finish in exchange. The superior finish is durable and more pleasing to look at and also offers greater protection.
If you are wondering if the process of metallic powder coating is different from the usual dry coating procedure, it is not. Just because the powder has been smooched with a tiny bit of the sparkly stuff doesn’t mean it requires special application techniques. In fact, here is a summary of the steps to take:
●Surface Preparation. Don’t make the mistake of rushing to spray your precious metallic powder coating on a dirty surface. Any oil, dust, or residue on the surface will prevent the powder from sticking properly so go ahead and clean the surface thoroughly then dry it properly.
●Electrostatic Spraying. Charge the metallic powder and spray it onto the surface. It’s best to use a fluidizing hopper instead of a box feeder as this will allow you to spray more evenly while feeding the gun a continuous stream of powder. Using a box feeder, especially with unbonded particles might make the flakes and pigments to clump together resulting in an uneven coat and undesirable surface
●Curing. Bake the object in an oven so the powder particles melt and fuse into a continuous and smooth coat
●Cooling and Inspection. Curing can take between 15 and 25 minutes depending on the type of powder. Once done, turn off the heat so the object cools down upon which it will be ready for inspection. Identify and remedy any imperfections.
While beauty is in the eyes of the beholder, metallic powder coating has been known to provide more than basic aesthetics. If you choose to coat the surface of your objects with metallic powder, the surfaces will benefit from the following:
●Increased Heat Resistance. Metallic powder coatings have a greater heat resistance property than conventional paints and thus find large applications in objects that are subject to high temperatures.
●Chemical Resistance. Objects with metallic powder coating resist damage from chemicals and solvents extremely well so that there is hardly any damage to their finishes upon exposure to harsh elements.
●Improved Scratch Resistance. The hard metallic effects and pigments make coats highly durable and provide better scratch resistance to valuable objects from daily wear and tear.
●Easy to Maintain: Metallic powder coating is non-porous and smooth preventing the accumulation of dirt, grime, and other adherent substances that bring about discoloration. Indeed, it’s easy to maintain the sparkly finish and keep it looking like new for years.
Metallic powder coating is much more than an emerging fresh trend in surface finishing; it is a progressive advancement in finishing technology. It offers unsurpassed aesthetics, enhanced durability, and at the same time is environmentally friendly.
Sure, some of the powder, especially the bonded type, may cost a bit more, but what you get in exchange is a durable and aesthetically pleasing metallic finish that’s easy to apply and maintain over the years. Talk to Ramseier Koatings specialists for the latest metallic powder coating solutions to make your life easier.